Pain points in industrial production
Digital Platform RIDP
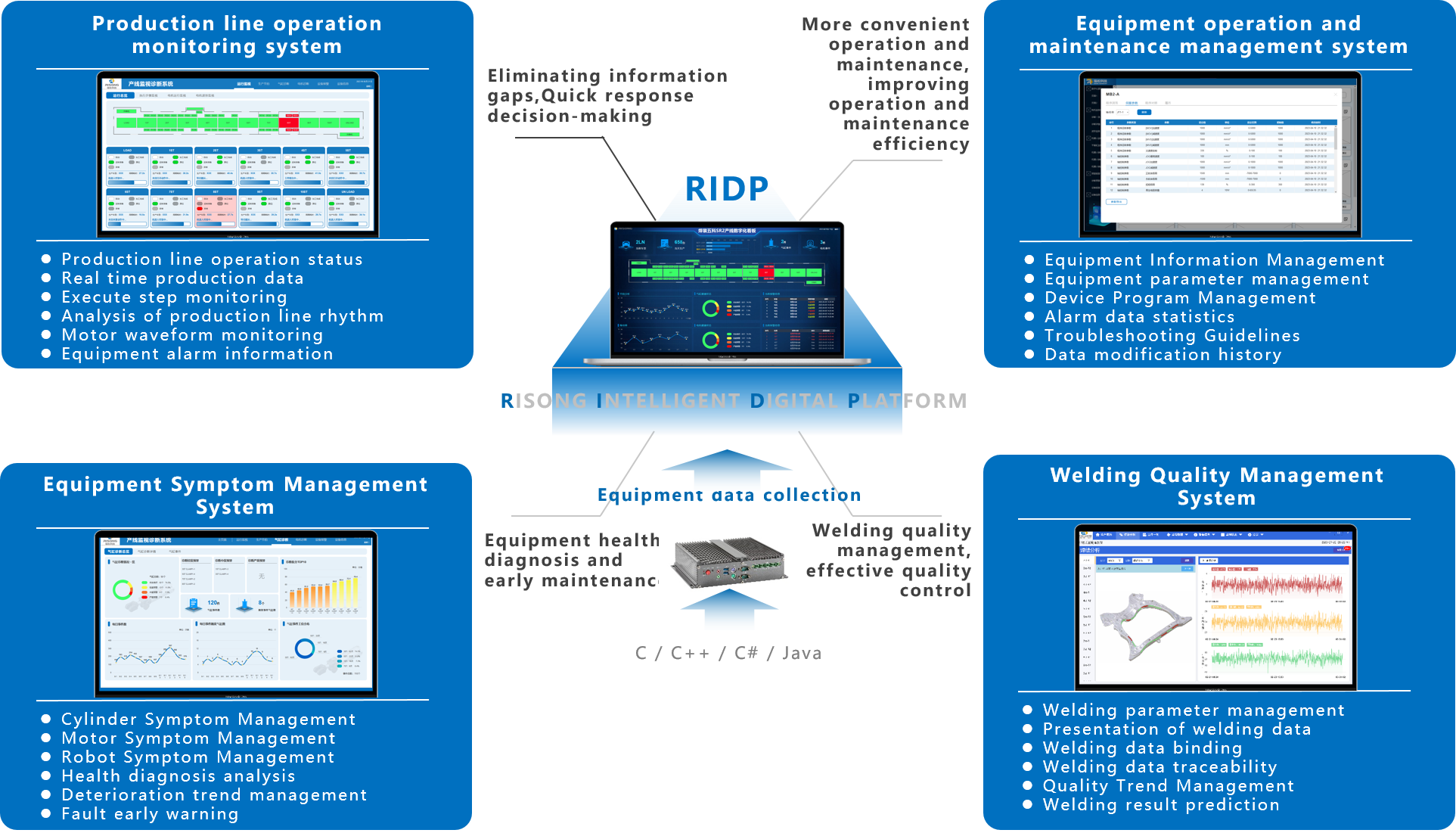
RIDP builds an edge data collection gateway and independently develops data collection service software by utilizing industrial internet and data collection technology to facilitate data exchange between OT and IT. By integrating IoT, eliminating data silos, equipment data collection, analysis, and application can be achieved, enabling various management functions such as production line operation monitoring, equipment maintenance management, equipment symptom management, and welding quality management.
IOT fusion, eliminating data silos
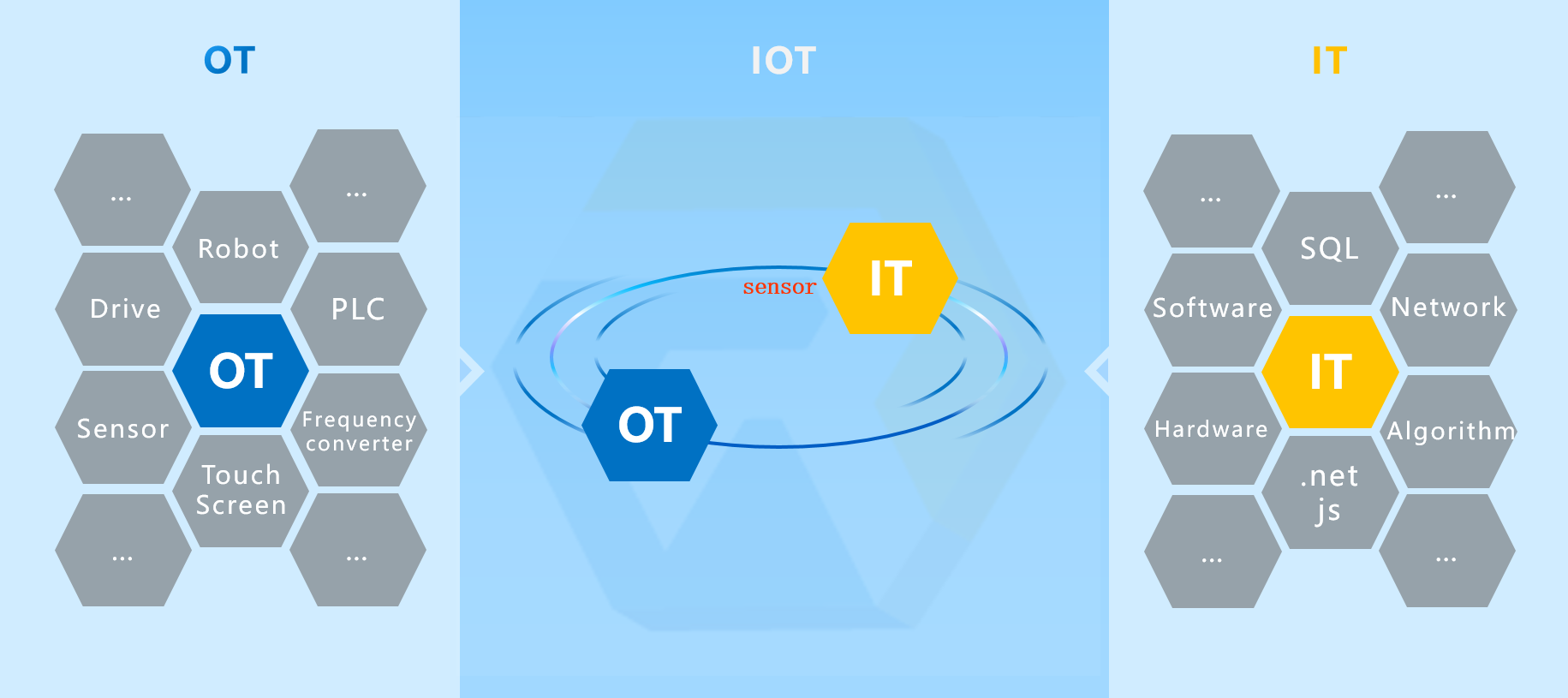
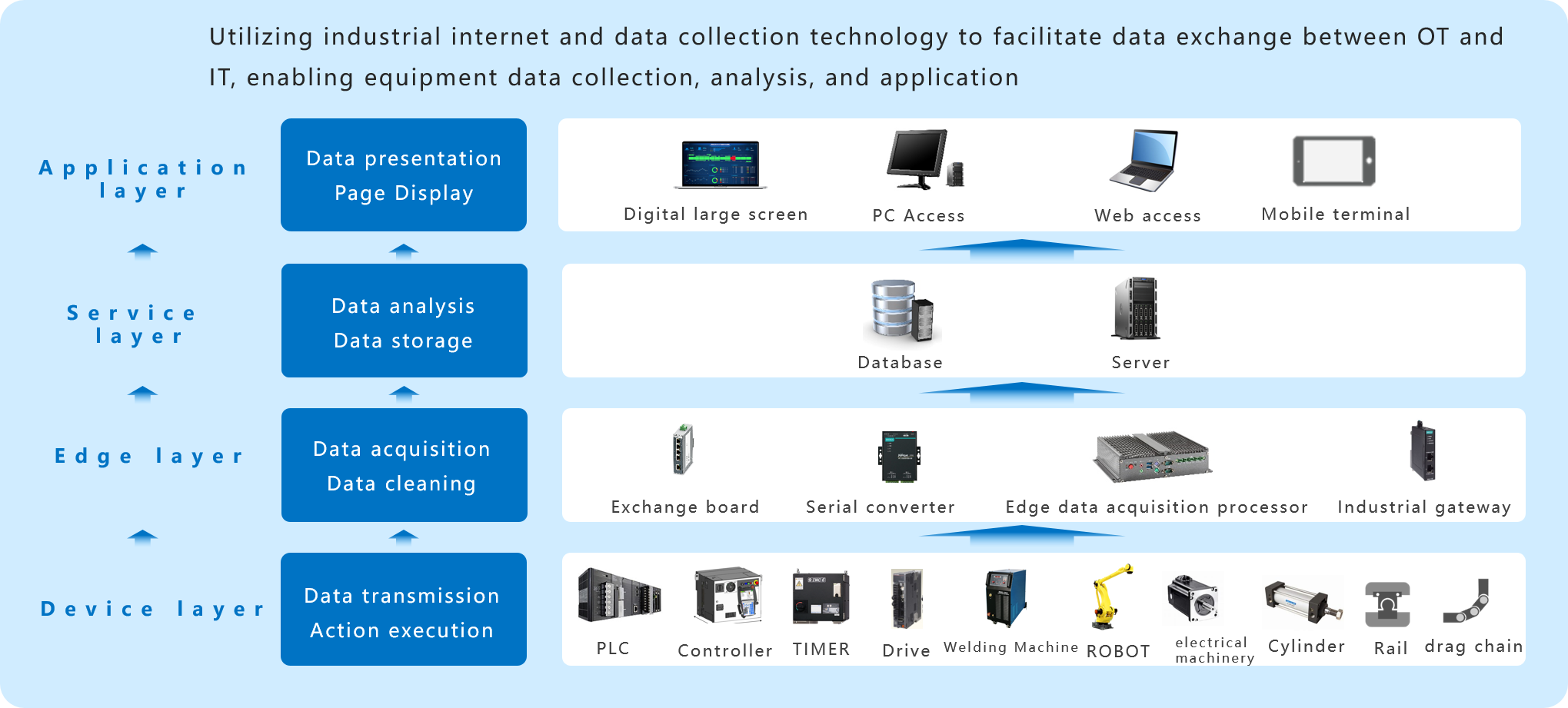
01
Production line operation monitoring

The production line operation monitoring system on the RIDP platform can monitor the overall operation status of the production line, achieve real-time fault alarms, closely monitor process steps, and transmit data for rapid fault localization and repair. The system can also provide real-time information on production rhythm, statistics on vehicle models, output, crop turnover rate, failure time, and other production data, eliminate information time differences, optimize production rhythm in a targeted manner, and improve production line efficiency.
02
Equipment operation and maintenance management
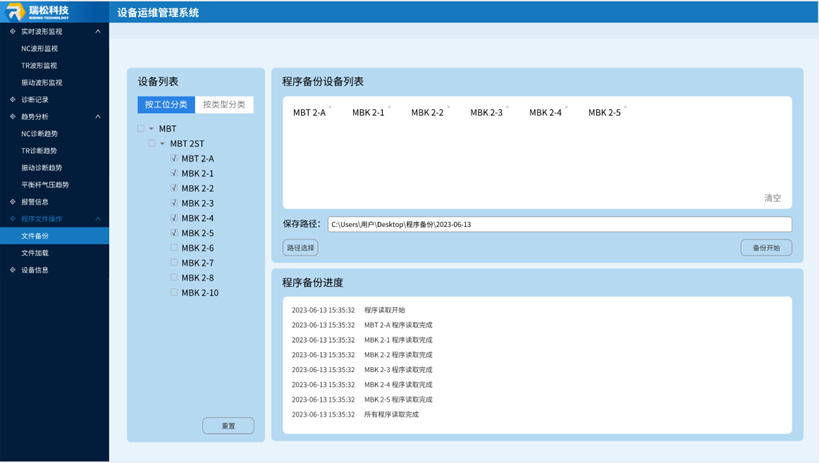
The equipment operation and maintenance management system on the RIDP platform can statistically analyze various dimensions of information such as workstations, alarm frequency, and downtime, facilitating the tracking of key faults, achieving visual management of alarm data, and ensuring data traceability. Users can backup robot programs with just one click on the system, quickly access pre-set fault help documents, various device information, program differential comparison tables, and other data. The system records various servo parameters, making it convenient for users to compare the historical modifications of parameters before and after, reducing communication costs for different personnel online work, and reducing the time for adding new equipment, achieving system management and improving efficiency.
03
Equipment Symptom Management
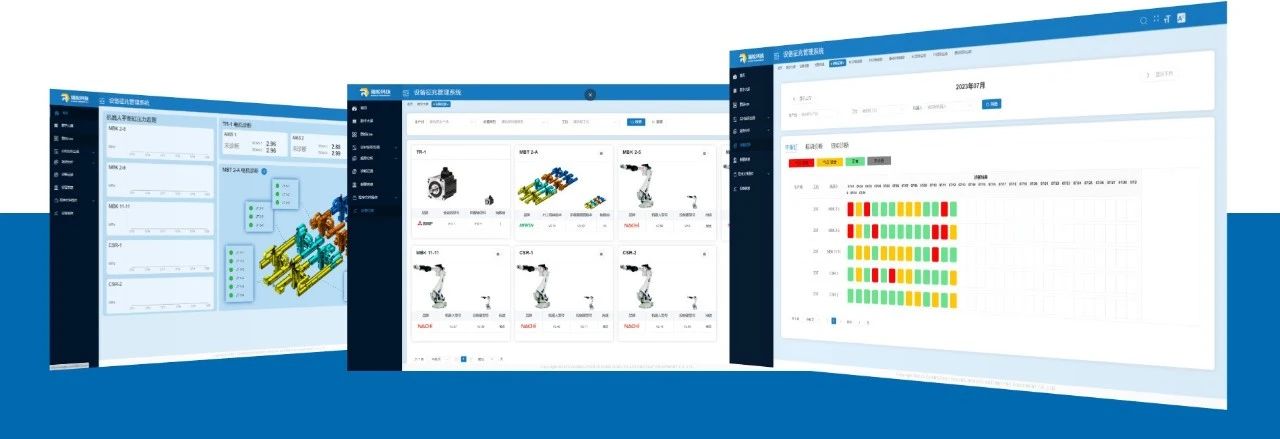
The device symptom management system on the RIDP platform can monitor the health status of devices in real time, strengthen the monitoring of sub healthy devices, prevent mechanical fatigue, and carry out regular and targeted maintenance to extend the service life and ensure smooth production. This system can analyze data of equipment such as cylinders, motors, and guides, compare historical data, monitor various data of the equipment in real time, and have a more comprehensive understanding of the equipment's health status, in order to set alarm thresholds and timely intervene manually.
04
Welding quality management

The welding quality management system on the RIDP platform collects information from robots, robot controllers, and production line PLCs using a server, establishes a database, and presents it visually to users. Users can use this information and pre trained AI models to formulate welding parameters, issue welding parameters, execute welding, predict quality, and other welding tasks, Scientifically and intelligently set the upper and lower resistance thresholds for welding quality products, as well as provide real-time warnings. This system can monitor and trace various welding processes such as arc welding and spot welding, facilitating analysis and utilization, effectively reducing production costs, and improving welding yield.
RIDP
Application cases
The industrial internet is empowering the digital transformation of various industries and has shown tremendous development prospects and strong support. The digital platform RIDP launched by Risong Technology will effectively promote data exchange and resource collaboration throughout the entire product process, production processes, and upstream and downstream of the supply chain, accelerate enterprise digital transformation, and assist in the high-quality development of intelligent manufacturing.
Recommend
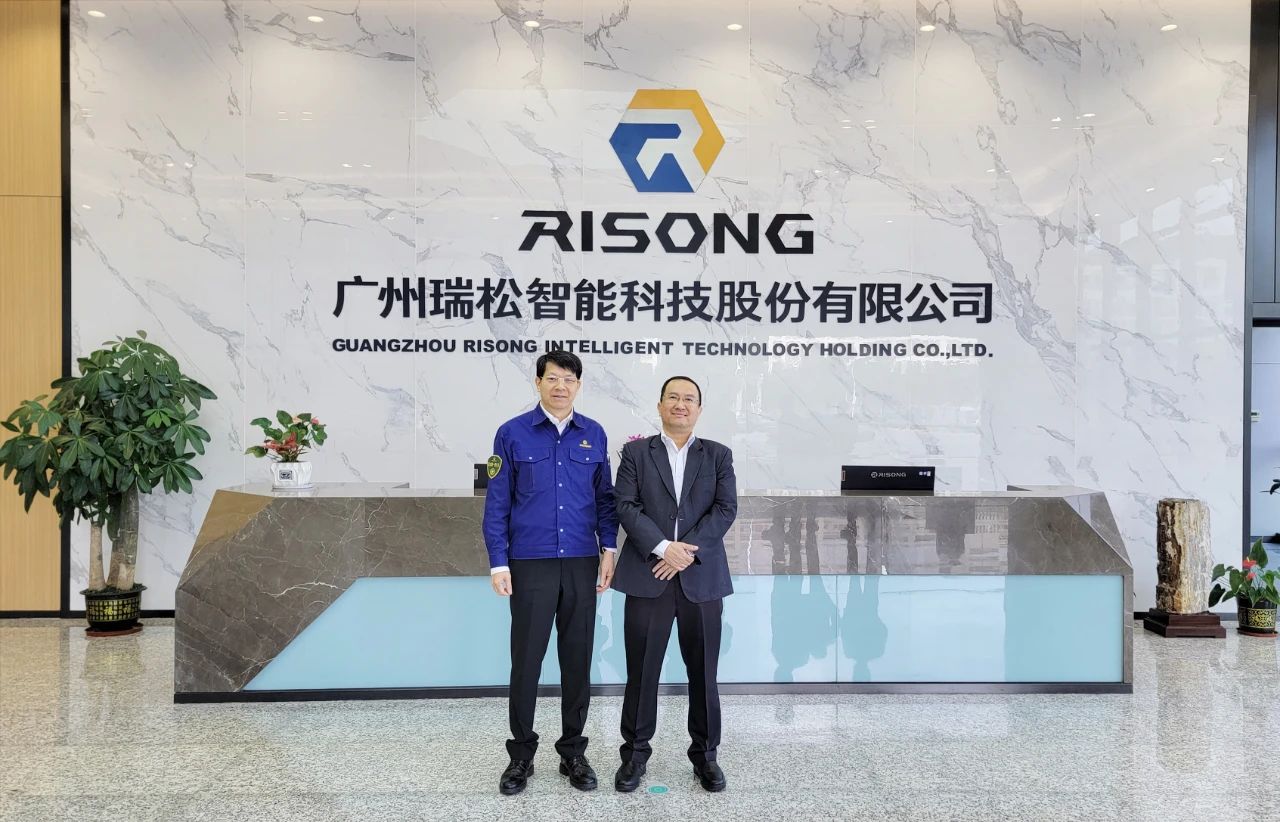
Malaysian auto parts manufacturer PHN visited Risong Technology
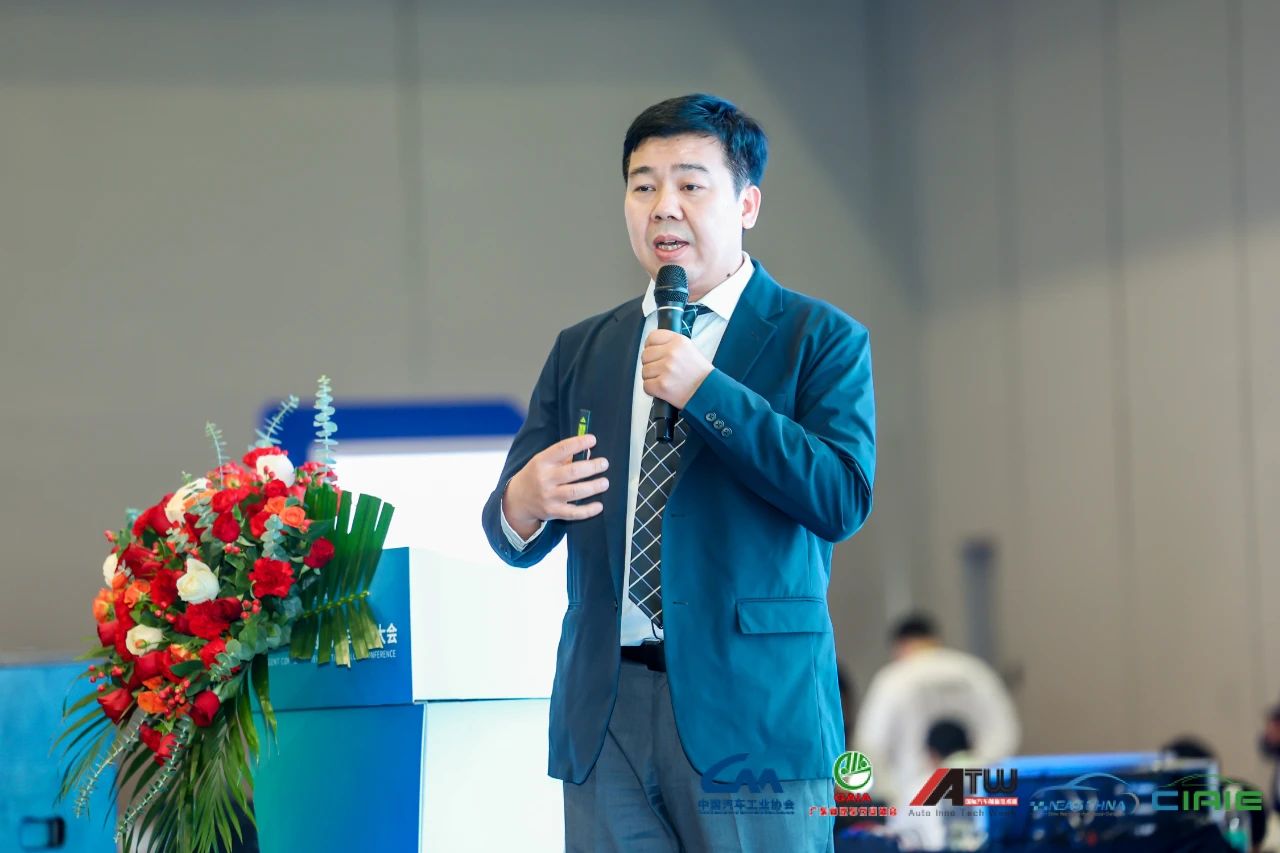
NEAS CHINA | Risong Hokuto participates in the 2023 China Automotive Supply Chain Innovation Achievement Exchange Jinan Greater Bay Area Interconnection Conference
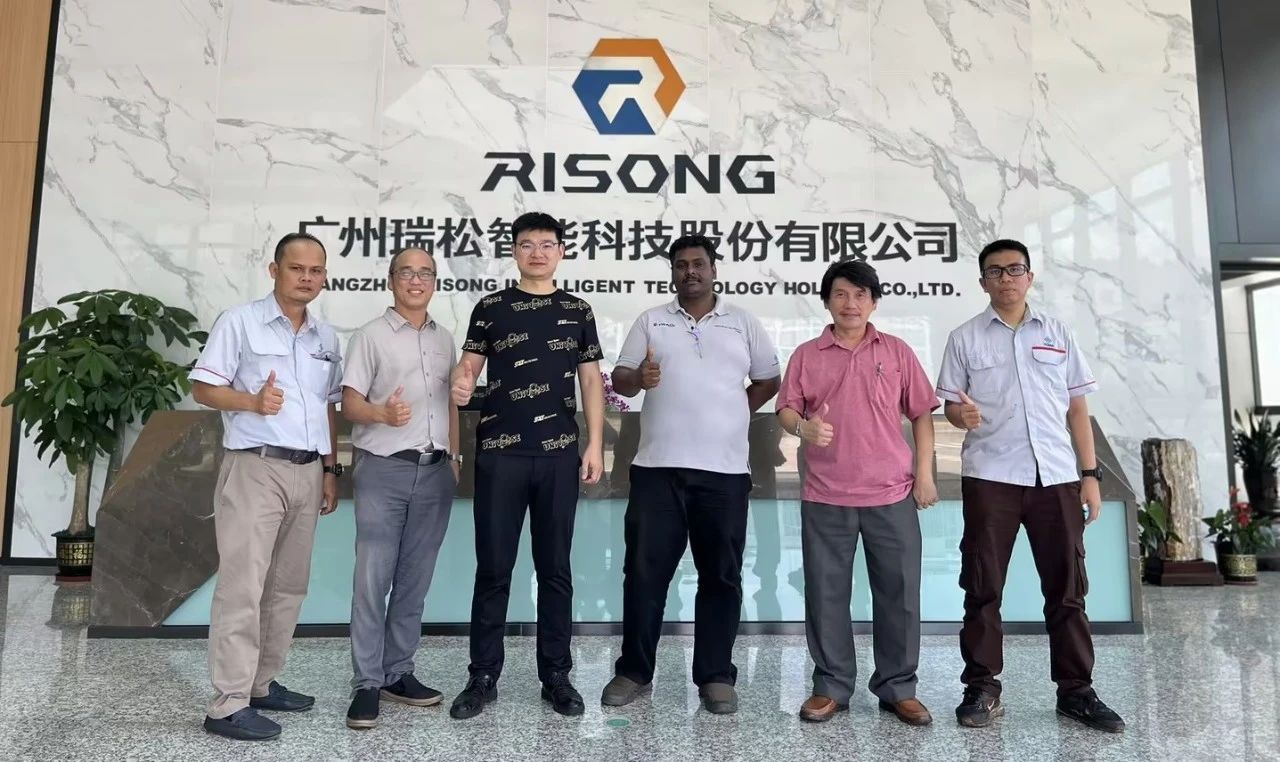
Risong Hokuto provides Malaysia's Chen Sing Group with an automotive manufacturing production line to explore global strategic development
More